In the world of packaging, standing still is not an option. From global brands to regional converters, companies are under increasing pressure to produce packaging that is not only functional, but also beautiful, sustainable, and fast to market. In this dynamic context, the flatbed die-cutting industry plays a critical role. And like the industries it serves — such as food, beverage, pharmaceuticals, cosmetics, and e-commerce — it is undergoing rapid transformation.
The global flatbed die-cutting market was valued at nearly USD 477 million in 2023, and it is projected to grow steadily to over USD 700 million by 2032, driven by a healthy CAGR of 4.5%. This growth isn’t just a number — it represents a wider shift in how packaging is conceived, produced, and consumed.
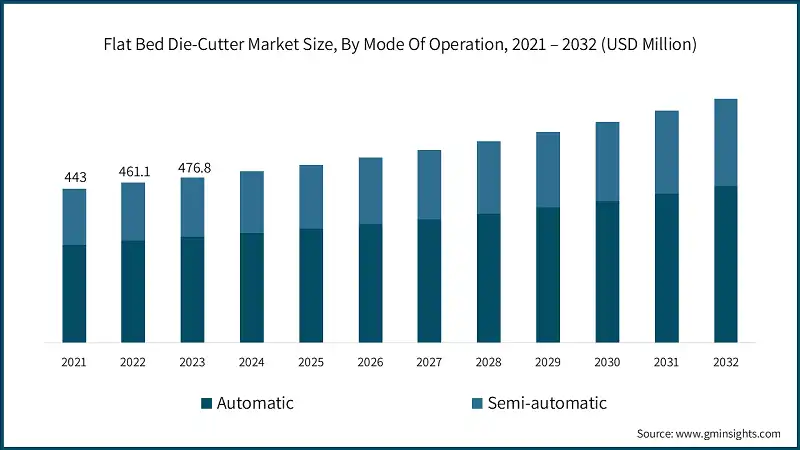
Brands today demand more than volume. They demand flexibility, customization, precision, and sustainability. The days of long runs with a single die are fading. In their place, we find short-run jobs, frequent changeovers, and complex designs that require high-performance machinery.
Customization is a key driver. Folding carton converters are increasingly expected to deliver tailored packaging for niche markets or product variants — often with extremely tight deadlines. The only way to keep up is with die-cutting equipment that offers both speed and agility.
Sustainability is another powerful force. Regulatory pressure and consumer awareness are pushing packaging manufacturers to adopt recyclable and biodegradable materials. Flatbed die-cutters must therefore adapt to handle a broader range of substrates — from lightweight papers to heavy corrugated boards — while minimizing waste and maintaining cut precision.
High initial investment costs, however, remain a barrier, especially for small and medium-sized businesses. This has created an opportunity for machinery manufacturers to deliver solutions that combine high-end performance with long-term reliability and low maintenance requirements.
Meanwhile, competition from alternative technologies, such as rotary die-cutters or digital laser systems, continues to intensify. While these technologies offer their own advantages in some applications, flatbed die-cutters remain the standard for quality, edge definition, and versatility — especially in folding carton production.
The Rise of Smart, Sustainable Machinery
Modern flatbed die-cutters are no longer just mechanical tools — they’re strategic assets. Innovations in machine construction, pressure control systems, feeder precision, and waste removal have allowed converters to:
• Reduce setup and job changeover times
• Maintain consistently high cut quality
• Lower scrap rates and reduce energy consumption
• Operate with smaller teams and lower technical barriers
But to meet these demands, not all machines are created equal. This is where DGM Technology comes into the picture — with its expertly engineered, highly reliable solution.
The Technocut 1050 S: DGM’s Answer to the Future of Folding Carton Die-Cutting
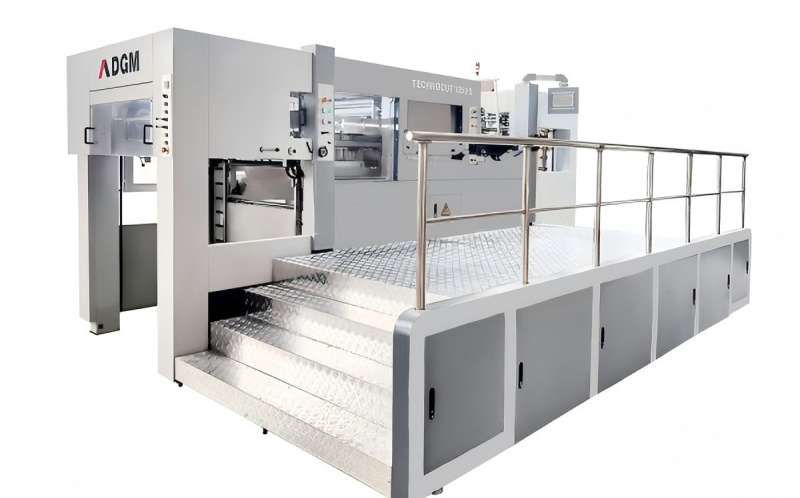
In this fast-paced, demanding environment, DGM Technology introduces the Technocut 1050 S — a flatbed automatic die-cutting machine with stripping, specifically developed for converters who prioritize precision, flexibility, and long-term performance.
Whether you’re processing paper as light as 80 g/m² or corrugated boards up to 4 mm, the Technocut 1050 S offers robust, consistent results. With a top speed of 7,500 sheets per hour and a 300-ton pressure system, this machine tackles the most demanding jobs without compromise.
Its cutting size of 730 x 1040 mm and high stack capacity make it perfect for large production volumes — but thanks to its quick-change tooling system and ergonomic touchscreen interface, it’s also incredibly effective for short-run, high-changeover environments.
Key Advantages of the Technocut 1050 S
√ High-Precision Feeding & Registration
A sophisticated feeder system equipped with suction cups, anti-static guides, and adjustable grippers ensures sheet stability and accurate positioning. This translates to fewer errors and minimal waste — even with complex materials.
√ Reinforced Cutting Platform & Cam System
The new main cam mechanism allows smoother movement of the platen and more uniform pressure distribution. Combined with a reinforced cutting base, this ensures long-term durability and cutting accuracy.
√ Integrated Stripping Section
The automatic stripping unit, with top and bottom pin frames, removes waste efficiently and cleanly. It speeds up finishing and reduces manual labor, keeping the machine in continuous motion.
√ True Non-Stop Operation
From a pre-stacker feeder to a curtain-based non-stop delivery, the entire system is designed for continuous workflow, reducing downtime and increasing output without sacrificing safety.
√ Modular, Human-Centered Design
Every aspect of the Technocut 1050 S has been engineered for the operator. From intuitive touchscreen controls and adjustable guides to quick-lock die plate systems and optional paper insertion devices — efficiency and usability are at its core.
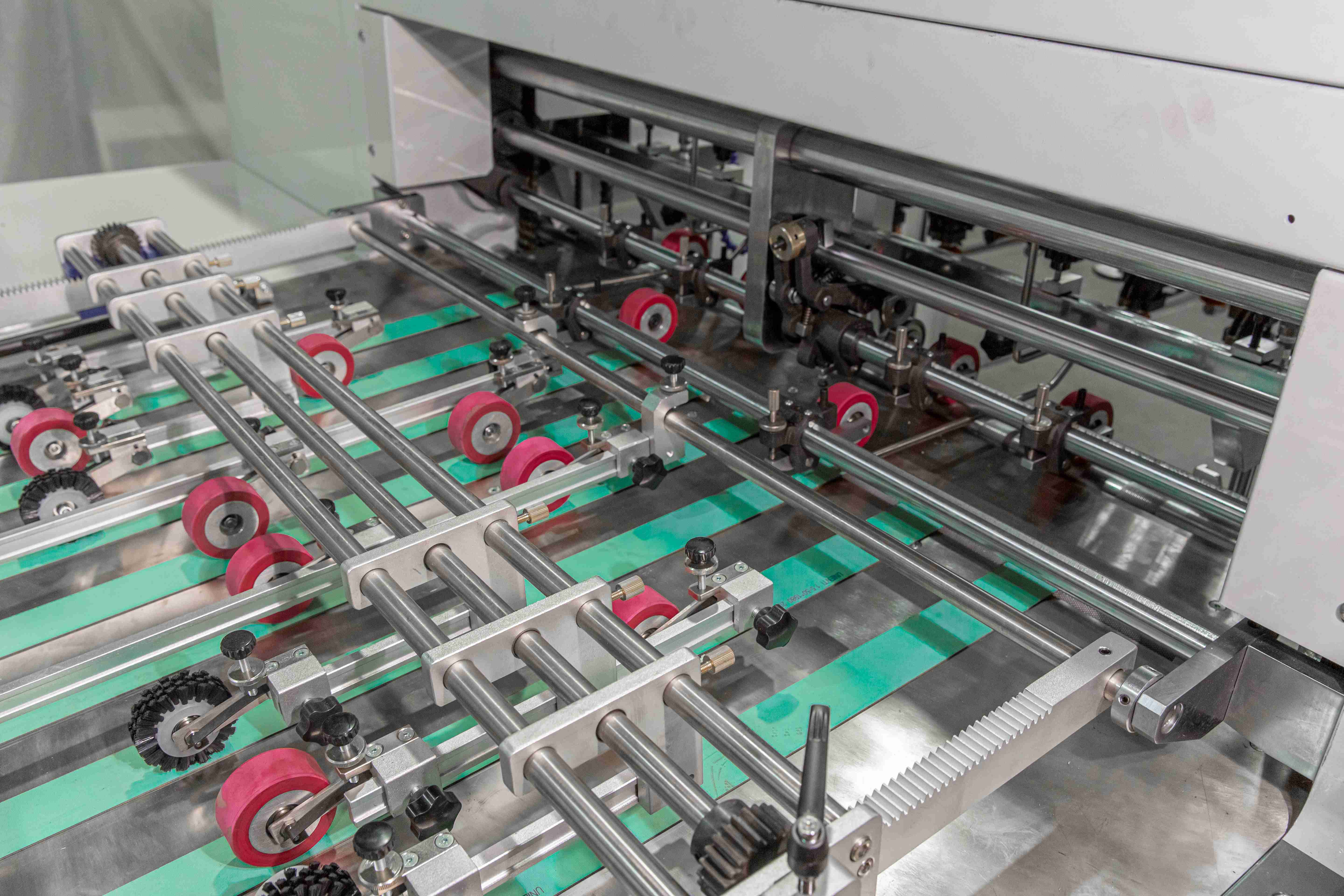
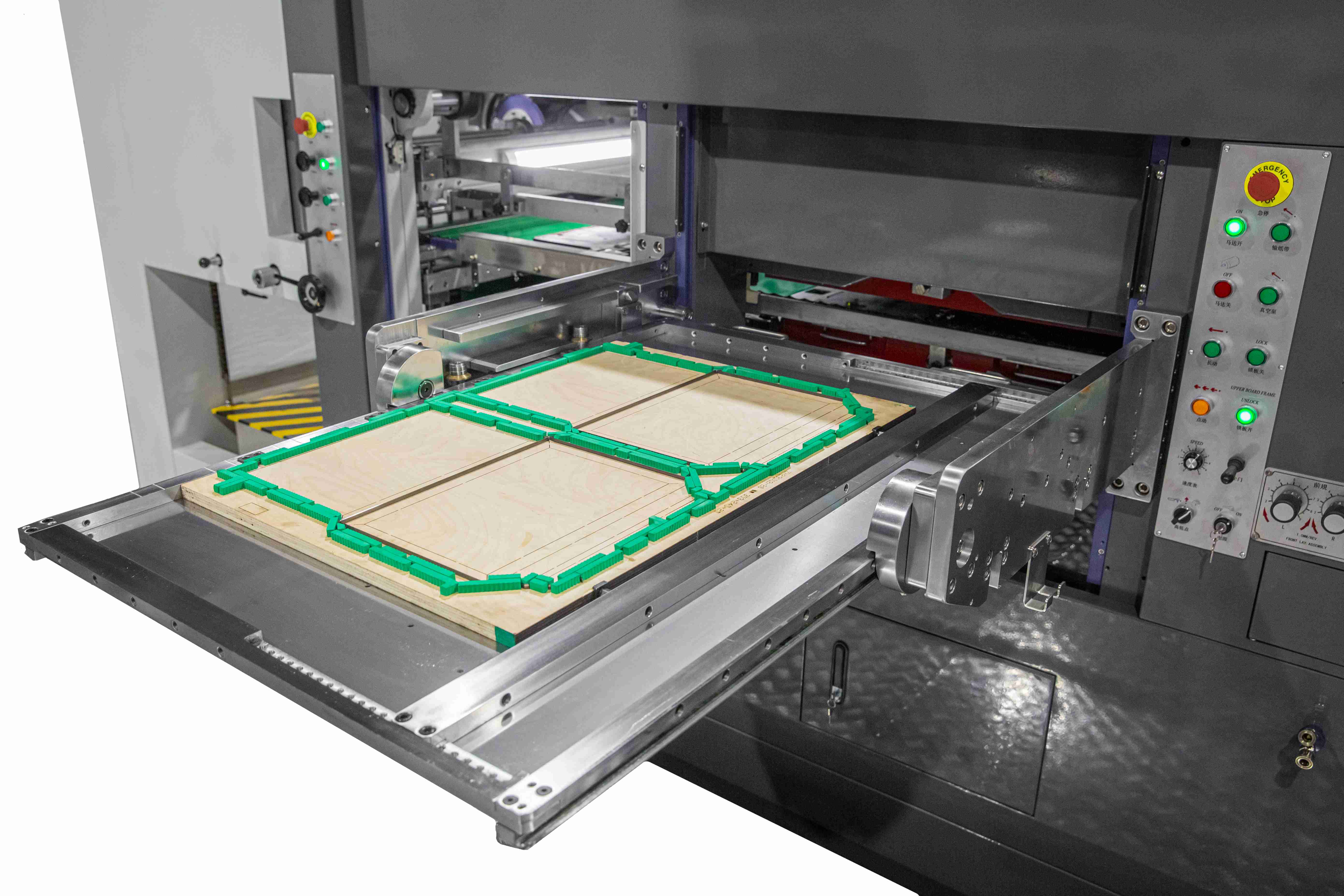
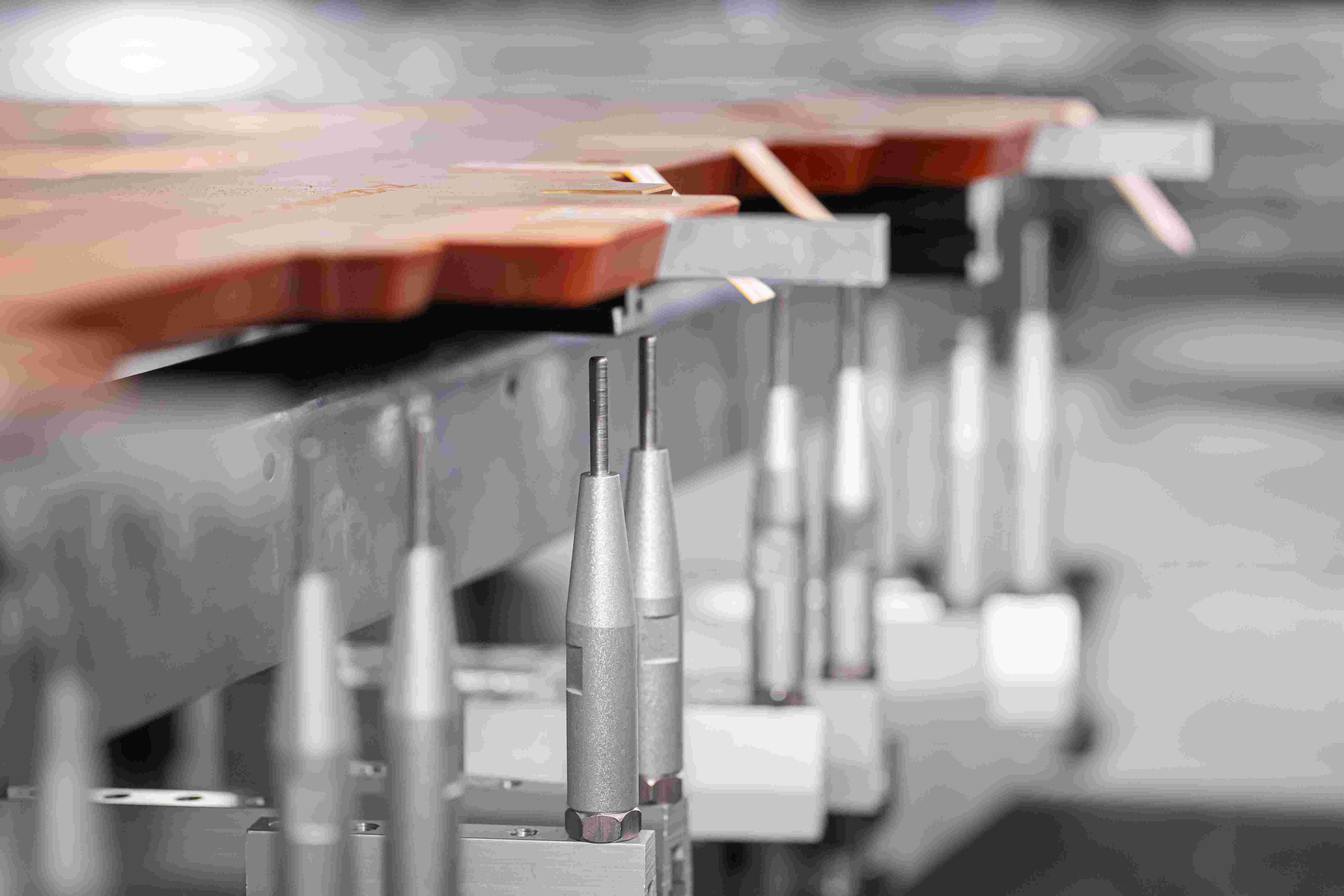
Built for the Markets That Demand the Best
• Luxury packaging (perfumes, cosmetics, electronics)
• Pharmaceutical cartons (precision critical)
• Food & beverage (hygiene and durability)
• E-commerce boxes and folding cartons (volume and variety)
Whether you need crisp creases, tight tolerances, or flawless waste removal — this is the machine that delivers.
The market is moving forward. So should your die-cutting.
The Technocut 1050 S is not just a purchase — it’s an investment in precision, flexibility, and competitive advantage.
Post time: May-06-2025