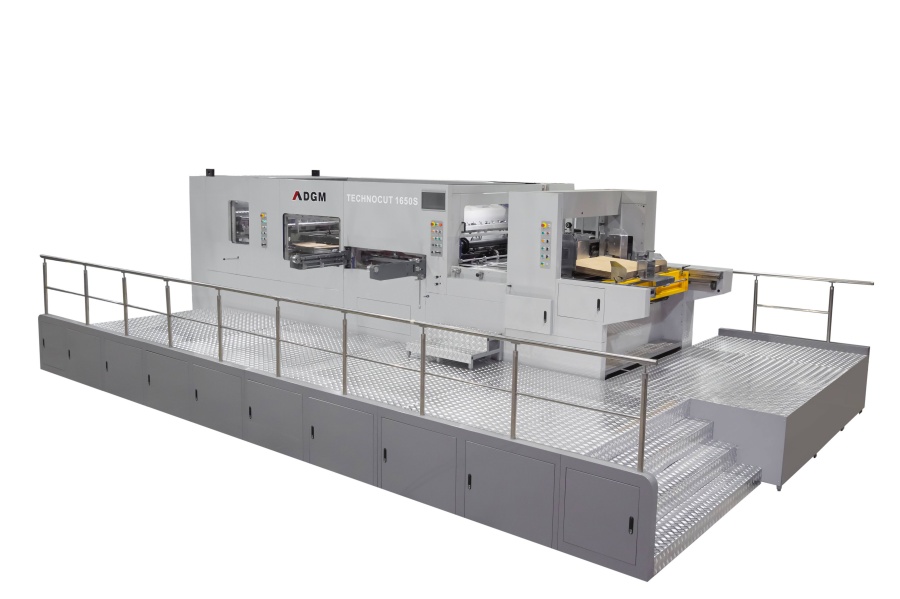
در سالهای اخیر، صنعت بستهبندی جهانی دستخوش تحول عمیقی شده است که با تغییر رفتار مصرفکننده، ظهور تجارت الکترونیک و افزایش پیچیدگی لجستیک جهانی شکل گرفته است. با افزایش ارسال مستقیم محصولات به مصرفکنندگان - از لوازم الکترونیکی کوچک گرفته تا لوازم خانگی بزرگ - تولیدکنندگان بستهبندی با فشار فزایندهای برای تولید راهحلهایی قویتر، بزرگتر و سازگارتر از همیشه مواجه هستند. بستهبندی موجدار به سرعت به مادهی انتخابی تبدیل شده است و ترکیبی نادر از دوام، تطبیقپذیری و پایداری را ارائه میدهد. در این زمینه، تقاضا برای جعبههای موجدار بزرگ که قادر به حمل ایمن کالاهای حجیم یا سنگین در زنجیرههای تأمین گسترده هستند، رو به افزایش است.
این روند، چالش جدیدی را برای صنعت تبدیل ایجاد کرده است: نیاز به پردازش مقوای موجدار با ابعاد بزرگ و استحکام بالا با سرعت و دقت بالا. دستگاههای برش قالب تخت سنتی که برای قالبهای استاندارد یا زیرلایههای سبکتر طراحی شدهاند، اغلب در مواجهه با مقوای دوجداره و سه جداره کم میآورند. چه در تولید کارتنهای لوازم خانگی، ظروف صنعتی یا بستهبندی صادراتی، تبدیلکنندگان اکنون باید جعبههای بزرگ تحویل دهند - و این کار را با تلرانسهای دقیق، حداقل ضایعات و حداکثر زمان آماده به کار انجام دهند. برای پاسخگویی به این چالش، DGM دستگاهی را از پایه مهندسی کرده است:تکنوکات ۱۶۵۰ اس، یک دستگاه برش تخت با کارایی بالا که معیار جدیدی را در تولید کارتنهای موجدار با ابعاد بزرگ تعیین میکند.
آنچه Technocut 1650 S را قابل توجه میکند، نه تنها مقیاس آن، بلکه توانایی آن در کار با ورقهای بزرگ و زیرلایههای ضخیم با همان چابکی و دقتی است که از دستگاههای کوچکتر انتظار میرود. این دستگاه که برای مبدلهایی که در محیطهای با حجم بالا کار میکنند ساخته شده است، میتواند مقوای موجدار تا ضخامت 10 میلیمتر، با اندازه ورق تا 1650 در 1200 میلیمتر و سرعت خروجی تا 6000 ورق در ساعت را پردازش کند. این دستگاه برای عملکرد بدون وقفه و دقیق در طول تولید طولانی طراحی شده است - ترکیبی از استحکام ساختاری با اتوماسیون پیشرفته.
فرآیند جابجایی ورق با یک سیستم تغذیه بسیار تطبیقپذیر آغاز میشود. بسته به نیازهای کاری، اپراتورها میتوانند بین تغذیهکننده تسمهای پایین، تغذیهکننده لبه سربی یا تغذیهکننده بالایی با سر مکش برای چاپهای بلند، یکی را انتخاب کنند. نازلهای مکش ضد خط و خش به محافظت از سطوح چاپ شده کمک میکنند، در حالی که راهنماهای جانبی موتوری و یک غلتک تغذیه سروو موتور، ترازبندی روان و دقیق را تضمین میکنند. یک سیستم تشخیص دو ورق، محافظت بیشتری در برابر خطاهای تغذیه، به ویژه هنگام انجام کارهای با ارزش بالا یا مواد چاپی، ارائه میدهد.
به محض اینکه ورق به میز ثبت رسید، دستگاه کنترل کامل را به دست میگیرد. شش تسمه با سرعت متغیر، تخته را حمل میکنند در حالی که لایههای کناری و جلویی آن را با دقت میکرومتری تراز میکنند. کل سیستم برای انعطافپذیری طراحی شده است - انواع مختلف تخته، پروفیلهای فلوت و طرحبندیهای پیچیده جعبه را با حداقل زمان راهاندازی در خود جای میدهد.
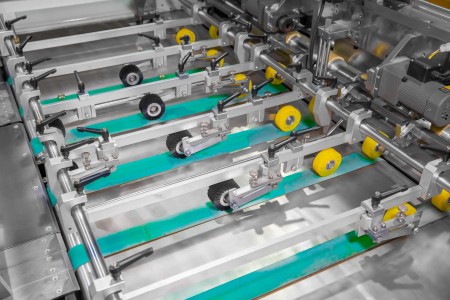
در قلب دستگاه تکنوکات ۱۶۵۰ اس، پرس برش قالبی آن قرار دارد که تا ۴۰۰ تن فشار وارد میکند. در اینجا، قدرت با ظرافت ترکیب شده است. اپراتورها میتوانند به راحتی عمق برش، فشار و ویژگیهای ایمنی را از طریق صفحه لمسی مرکزی HMI مدیریت کنند و نتایج ثابتی را در شیفتها و اپراتورها تضمین کنند. سیستم تعویض سریع قالب برش، سیستم موقعیتیابی مرکزی و قفل پنوماتیک، همگی به تعویض سریع و دقیق و کاهش زمان از کارافتادگی کمک میکنند - مزایای کلیدی در محیطهای رقابتی که انعطافپذیری به اندازه حجم تولید اهمیت دارد.
یک بخش مخصوص لایه برداری پس از پرس برش قرار دارد که استخراج ضایعات را با سرعت و دقت انجام میدهد. این سیستم شامل یک مکانیزم مرکزی و دستگاه استخراج برش، با کنترلهای لمسی برای سادهسازی تنظیمات است. ویژگیهای ایمنی داخلی از اپراتورها و تجهیزات محافظت میکند و عملکرد روان و ایمن را حتی در شرایط کار مداوم تضمین میکند.
ورقهای تکمیلشده به بخش تحویل منتقل میشوند، جایی که یک سیستم پرده موتوری، تولید بدون توقف را امکانپذیر میکند. جاگرهای جانبی و جلویی به تشکیل پشتههای تمیز و مربعی کمک میکنند، در حالی که پشتهساز از ارتفاع تا ۱۴۰۰ میلیمتر پشتیبانی میکند و نیاز به تخلیه مکرر را کاهش میدهد. اپراتورها میتوانند فرآیند تحویل را از یک HMI ثانویه در انتهای خط کنترل و تنظیم کنند، که به طراحی کاربرپسند دستگاه میافزاید.
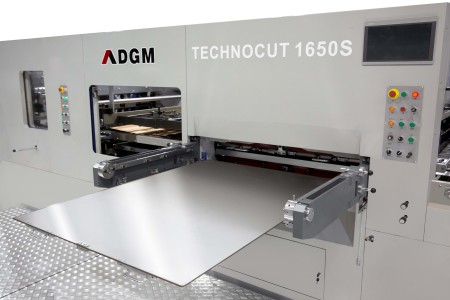
نکات برجسته عملکرد کلیدی:
• حداکثر اندازه ورق: 1650 x 1200 میلیمتر
• حداکثر ضخامت تخته: تا 10 میلیمتر (شامل دیوار سهجداره)
• حداکثر سرعت: 6000 ورق در ساعت
• فشار برش: ۴۰۰ تن
• حداکثر اندازه برش قالبی: ۱۶۶۰ در ۱۱۸۰ میلیمتر
• حاشیه گیرش: تا 6 میلیمتر، حداقل ضایعات با لایهبرداری کامل
• ارتفاع پشته در زمان تحویل: تا ۱۴۰۰ میلیمتر (شامل پالت)
• تعویض سریع قالب و قفل پنوماتیک برای کاهش زمان آمادهسازی
• صفحات لمسی HMI در ایستگاههای کلیدی (تغذیه، برش قالب، تحویل)
• تشخیص از راه دور و روغن کاری خودکار برای کاهش زمان از کار افتادگی
فراتر از خروجی خام، آنچه واقعاً Technocut 1650 S را متمایز میکند، تمرکز آن بر کارایی و دوام است. هر عنصر دستگاه - از میلههای آلیاژی با استحکام بالا گرفته تا سیستمهای محافظت در برابر اضافه بار و روغنکاری خودکار - به گونهای طراحی شده است که طول عمر را افزایش دهد، تعمیر و نگهداری را کاهش دهد و عملیات را روان نگه دارد. تشخیص از راه دور، آرامش خاطر و پشتیبانی سریع را حتی از تکنسینهای خارج از سایت ارائه میدهد.
در صنعتی رقابتی که فرمتهای بستهبندی بزرگتر، زیرلایهها پیچیدهتر و برنامههای تولید فشردهتر میشوند، Technocut 1650 S به عنوان یک راهحل تعیینکننده خودنمایی میکند. این دستگاه به مبدلها، مقیاس مورد نیاز، دقت مورد انتظار و اتوماسیون مورد نیازشان را - همه در یک پلتفرم قابل اعتماد - ارائه میدهد.
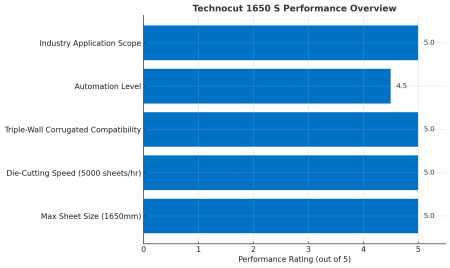
اگر کسب و کار شما آماده گسترش به بستهبندیهای موجدار با فرمت بزرگ است، یا به دنبال جایگزینی سیستمهای برش قدیمی با چیزی سریعتر و توانمندتر هستید، Technocut 1650 S عملکردی بدون نقص ارائه میدهد. این دستگاه نه تنها با صنعت بستهبندی همگام است، بلکه سرعت آن را نیز تعیین میکند.
زمان ارسال: ۲۴ ژوئن ۲۰۲۵